Digitalization in Industry 4.0 covers all business processes. However, this will by no means eliminate human labor. Nonetheless, it will need to redefine itself. To implement real-time data sharing and networked production, teams combining the various disciplines will monitor processes and spearhead their value creation.
The video is loading...
Simulation for test and approval. Befor builiding up the real final solution, all processes can be optimized til they are perfect by Lean.
It is the close networking of industrial processes with cutting-edge IT technologies with the aim of creating a smart factory. In applying this production philosophy, Industry 4.0 will bring about a future convergence of the real and the virtual worlds. This approach promises to lead to completely new production methods and processes. What’s new about this approach is that it is not just machines and integrated systems that will communicate with one another. As part of Industry 4.0, all systems will be intelligently networked and will also exchange real-time information with the products to be manufactured.
Discover the future plant with Industry 4.0
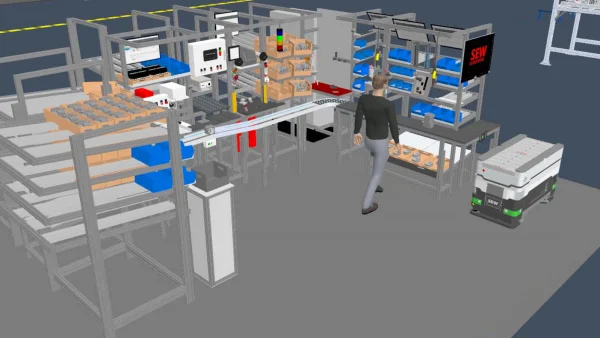
Industry 4.0 lets you plan and then tour the new plant virtually already before building your production environment. This is made possible by simulating and emulating the individual process steps true to detail. Next, your entire plant is simulated in the software and you can then directly "take a tour" of the plant using VR goggles. The simulation is so intelligent that the assistance systems will respond to your position – if you block the travel path, the assistants will stop just as they will do later in the real plant. The assistants will not continue their travel until you go to another position in the simulated production area.
We are using our real-time simulations as early as the planning stage so as to check with customers the viability of systems, processes and workflows before they are constructed or taken into operation. This has the considerable advantage that any errors can be identified and eliminated as early as the planning phase. It also gives rise to customized solutions early on, which customers can implement in cooperation with SEW. This makes processes more reliable, and any wastage can be identified early on.
We create a virtual system based on real environment, production and design data that exactly reflect the processes of the planned system. The simulation can be used in such a way that all processes, also regarding the controller, can be optimized until a perfect condition is attained. Thanks to virtual reality, each detail of the system is accessible and can be tested.
When the customer accepts the system at this point of time, we start transferring the data gained from simulation to the real system. Doing so will not only significantly decrease the time required for startup but also minimize risks.
Implementation of the Sm@rtFactory concept
The video is loading...
In Virtual Reality, all aspects of operation and processes can be performed in real time.
This is also the case at SEW itself. We're currently expanding our showcase factory at the Graben-Neudorf site for further products. The next smart factory is based on the first. It isn't just the processes and systems that have been optimized in many different details – the new showcase factory now has all the elements, including a fully automated oil filling station and a paint shop.